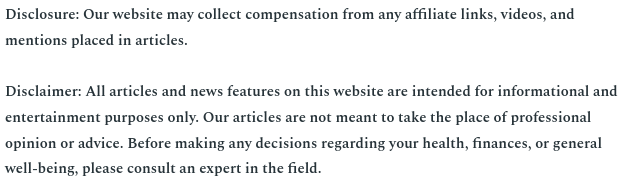
Random tower packing is a widely used method in various industrial applications, primarily in chemical processing plants. Its importance has surged due to its crucial role in enhancing the efficiency and effectiveness of mass transfer operations. Increasing interest in random tower packing is attributed to its versatility and ability to improve throughput in processes involving gas-liquid contact.
This method is gaining momentum as industries strive to optimize their operations while reducing costs. With advancements in material science, the range of applications for random tower packing has expanded, making it a vital component in modern industrial systems. As a result, understanding its purpose and functionality has become more important than ever.
What is Random Tower Packing?
Definition and Purpose
Random tower packing refers to the use of small, randomly arranged pieces within a tower or column to facilitate contact between phases, typically gas and liquid. Its primary purpose is to improve mass transfer efficiency compactly and cost-effectively. This method allows for better distribution of liquid across the column, ensuring more surface area is available for the gas-liquid interaction. The random orientation of packing materials disrupts flow channels, thereby enhancing mass transfer rates. In industrial settings, random tower packing is often selected for its ability to handle varying flow rates while maintaining operational stability and efficiency. As such, it is a popular choice for industries focusing on optimizing efficiency in chemical processing.
History and Development
The development of random tower packing dates back to the early 20th century when the need for efficient phase contactors became prominent. Over time, innovations have led to the creation of more sophisticated and varied packing materials. Initially, materials like ceramics and metals were predominantly used, but advancements have introduced plastics and other modern composites. This evolution has been driven by a demand for materials that offer higher efficiency and lower operational costs. Research and continuous experimentation have allowed engineers to refine random tower packing design, adapting it to current industrial needs.
Why is Random Tower Packing Used in Industry?
Efficiency in Chemical Processes
Random tower packing is crucial in enhancing the efficiency of chemical processes by maximizing the interaction between gas and liquid phases. This interaction is essential in processes such as distillation, absorption, and stripping operations. The packing material increases the surface area available for gas and liquid to interact, facilitating better mass transfer rates. This efficiency is a key objective in industrial processes where optimizing throughput and product quality are priorities. In essence, random tower packing contributes to operational efficiency by reducing energy consumption and improving process yields.
Cost-Effectiveness
One of the major reasons for the widespread adoption of random tower packing is its cost-effectiveness compared to structured packing solutions. Its low production cost and ease of installation translate to reduced capital and operational expenses. Moreover, random tower packing is versatile and adaptable, making it suitable for retrofitting existing structures with minimal modifications. This adaptability reduces the need for extensive infrastructure changes, further cutting costs.
How Does Random Tower Packing Work?
Mechanism of Action
Random tower packing works by randomly distributing packing materials within a column to disrupt and redistribute liquid flow, thus improving mass transfer. The packing materials themselves provide surfaces that facilitate gas-liquid interactions. This mechanism ensures that the liquid flows evenly and maximizes contact with the upward flowing gas, enhancing the efficiency of mass transfer. Consequently, the packing arrangement helps achieve a more uniform mass exchange across the column. Random tower packing’s effectiveness relies on varying sizes and shapes of the packing materials, promoting turbulence and resulting in improved interaction between phases.
Design Considerations
Design considerations for implementing random tower packing focus on material selection, column dimension, and arrangement within the column. A suitable design ensures that the packing delivers optimal performance under specific operational conditions. Factors like pressure drop, flooding point, and efficiency must be evaluated to tailor the packing configuration for the desired process outcome. These considerations are crucial to maintaining the delicate balance between performance and efficiency.
What Are the Different Types of Random Tower Packing Materials?
Material Types and Properties
Random tower packing materials vary widely, with ceramics, metals, and plastics being the most common. Each material type offers distinct properties, like thermal resistance, chemical compatibility, and mechanical strength. Ceramic materials are often chosen for their high heat and corrosion resistance, which is advantageous in harsh chemical environments. Metals, on the other hand, provide higher structural integrity and are typically used in high-load applications. Plastics are increasingly popular due to their lightweight nature and cost-efficiency, making them suitable for less demanding environments.
Selection Criteria
Choosing the appropriate random tower packing material involves evaluating factors such as chemical resistance, temperature tolerance, and mechanical durability. These criteria ensure that the packing material will perform effectively within the intended application. Environmental factors like pressure conditions and the nature of the chemicals being processed also play a significant role in material selection. Ensuring compatibility with these conditions is crucial to preventing material degradation and maintaining efficiency.
What Are the Challenges and Limitations of Random Tower Packing?
Operational Challenges
Operational challenges associated with random tower packing include issues such as fouling, pressure drop, and mechanical damage. These challenges can lead to reduced efficiency and require careful monitoring and maintenance. Fouling, the accumulation of unwanted material on packing surfaces, can significantly impact efficiency by reducing the available surface area for gas-liquid interaction. This challenge necessitates regular cleaning and monitoring to maintain performance.
Limitations and Solutions
While random tower packing offers many benefits, it also has inherent limitations, such as a lower capacity compared to structured packing. This limitation can affect the feasibility of random packing in high-capacity systems. To overcome these limitations, industries may consider hybrid systems that combine the strengths of both random and structured packings. Such approaches help enhance overall system performance and efficiency. Continuous innovation in material science and design also paves the way for addressing limitations, pushing the boundaries of what random tower packing can achieve.
.