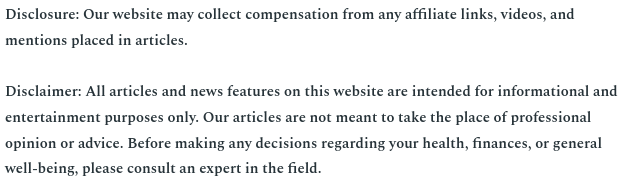

Have you decided to look into the benefits of getting a custom roto mold for your project? Well, we wanted to help you understand how these work and provided you with a list of great benefits that Rotomolding can provide you with.
- Design Flexibility
Custom roto moldering pieces are designed to made designed and manufactured to fit every space available. This means that no matter the size of the project, you know you can get good custom rotational molding. In addition to this, these bulk containers help with consolidating all of the pieces of your project into one rotomolding. This means fewer pieces to deal with, giving you a lesser chance of failure in the industry.
- Superior Strength
One of the notable perks of a custom roto mold parts is their superior strength versus other molding types. This can be attributed to several things including corrosion-resistance material, one-part construction, durable plastic and even wall thickness in every piece. This makes this a must-have for your projects.
- Easier to Modify the End Result
Honestly, custom roto mold parts are extremely simple to make because the equipment is simple to use, unlike some other types of molding ? such as blow molding and thermos-forming mold. This means that you can easily make minor adjustments to your mold to help with accommodating to new needs. As a business owner, you want to make sure that you have the opportunity to tweak things as needed.
- Consistent Wall Thickness Makes it Perfect
The consistency involved with the wall thickness makes it more notable for a must-have in custom roto molding. Traditionally, metals are known for being weaker on the corners versus anywhere else. This is because this is where the most stress is involved in the structure. With other types of molding, it?s impossible for you to get a wall thickness that fits perfectly for you. However, this is not the case with the roto mold. Rotomolding offers you the consistent wall thickness you seek because of the constant rotation. This helps with allowing the resin to coat evenly, giving you the best mold walling with even walls.
- Short Production Time Vs the Competition
Comparing this to the next shortest production time molding, injection molding, it takes half the time for rotomoldings to be performed. Injection molding takes, on average, about six (6) months to complete the project ? and it can be even longer in larger projects. With rotomoldings, most companies are able to distribute these out within 3 months ? this includes the design process, tooling process and production of the product. Who knew that you could get such convenient timing with your project right around the corner?
Rotomolding Triumphs the Competition
You want reliability when you are working with a huge project. Using plastic, that?s tested sturdy, custom roto mold parts are the ideal way for you to expand your project quicker and with more reliability. Why wait six months to have a product that will have uneven walls and poor overall quality when you could have had it in half the time with twice the strength, durability and evenness and thickness with your walls.