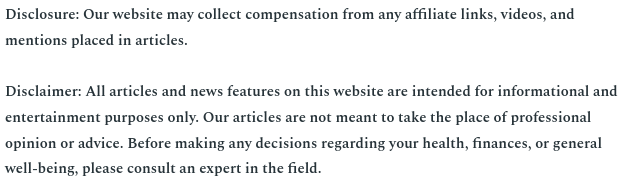
Mill liners are critical components in grinding mills, serving to protect the mill’s interior and optimize the grinding process. Regular mill liner inspection is essential to ensure the liners are functioning correctly and to prevent costly downtime. But how exactly are these inspections carried out?
The first step in mill liner inspection is a thorough visual examination.
This involves checking for obvious signs of wear, such as cracks, dents, or missing sections. Visual inspections can reveal early signs of damage that could lead to more severe problems if left unaddressed. Operators often conduct these inspections regularly to catch any issues early.
In addition to visual checks, thickness measurements are taken using tools like ultrasonic thickness gauges. These measurements help determine the rate of wear on the liners and predict their remaining lifespan. If the thickness falls below a certain threshold, it may indicate that the liners need to be replaced to avoid potential failure.
Non-destructive testing methods, such as magnetic particle testing or dye penetrant testing, are also used to detect hidden cracks or defects that might not be visible during a visual inspection. These tests are particularly useful for identifying subsurface issues that could compromise the liner’s integrity.
Lastly, analyzing the mill’s performance data, such as grinding efficiency and output, can provide indirect indicators of liner wear. A drop in performance may signal that the liners are no longer effective and require a closer mill liner inspection.